Blog
Beyond the Batteries: The Importance of Worker Safety and Training in Energy Storage
January 13, 2025
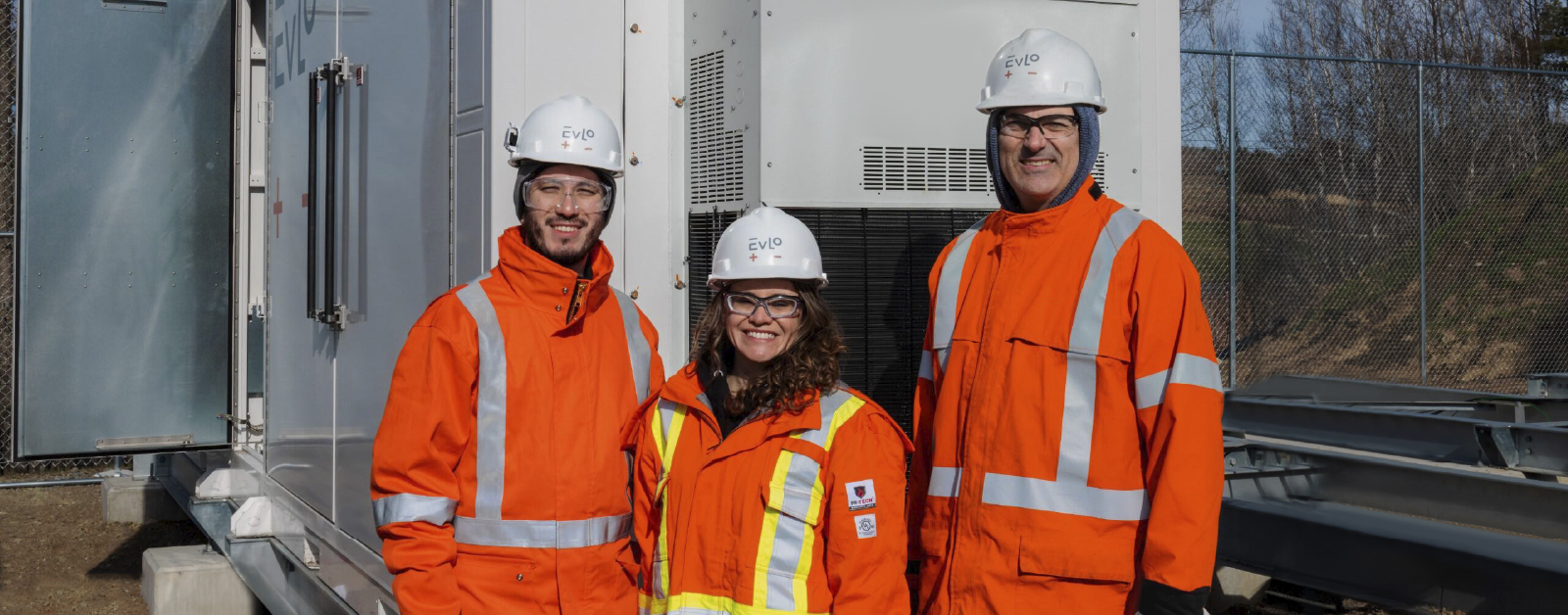
As utility-scale battery energy storage system (BESS) projects grow in both size and prevalence, expectations for performance, safety, and longevity must grow along with them. While multiple layers of protection are required when working in any high-voltage scenario, every BESS project presents unique safety considerations that demand meticulous planning and preparation across design, integration, assembly, and construction.
Given the projected doubling of the BESS market by 2030, it is imperative to evolve, adhere to, and scale safety training to accommodate a growing workforce and bridge skill gaps. As an experienced, fully integrated BESS solutions provider, EVLO is committed to worker safety at every step, from product design through deployment and maintenance.
In this blog, we will cover:
- How worker safety begins at the product design stage
- Embedding safety protocols into every project site
- Creating a site-specific emergency response plan
- Key elements of proper stakeholder training
- How EVLO’s test line strengthens best practices for worker safety across the industry
Safety by Design
Careful product design sets the foundation for worker health and safety throughout the project lifecycle. We take extra care in the design stage, conducting the critical upfront work to ensure every project is equipped with a system that will perform safely in a variety of real-world conditions.
In the case of EVLOFLEX, we’ve incorporated leading safety features at all levels – including the cell, module, rack, tray, and enclosure – to protect against thermal runaway that can result in fires if not adequately addressed. The EVLOFLEX system also employs both active and passive ventilation methods, exceeding NFPA 69 design standards to ensure passive gas evacuation even during power outages.
Both EVLOFLEX and EVLO SYNERGY are fully integrated solutions. Our customers don’t have to piece their systems together from various suppliers, mitigating integration challenges that can impact worker safety. Furthermore, every project is supported by our EVLOGIX energy management system (EMS), which features advanced monitoring and control systems to detect early signs of battery failure or overheating. This critical real-time data and alerts at customers’ fingertips helps to proactively address incidents before they escalate.
No Confusion Means Smooth Execution: Safeguarding Workers at the Project Site
While thoughtful product design is paramount to project safety, it is just one element of the overall equation. Project partners must also take every available measure to inform and protect onsite workers.
Exacting worksite procedures ensure that clear safety protocols, tailored to the specific needs of a given site, are put in place from day one. EVLO’s prevention program doubles down on worker protection, backed by meticulous documentation.
At our project sites:
- A health and safety worker must be present at all times
- All activities require proper documentation
- Every task is guided by safety measures and necessary sign-off from workers
- A “lock out and tag out” system prevents confusion and ensures the secure and seamless transfer of information across project phases
Each step in EVLO’s process also includes a safety ‘gate’ to ensure proper safety protocols are followed. Every unit installed on our test line or used for customer demonstrations is carefully commissioned, just as they are on customer sites, with proper grounding and safety protocols.
While baseline safety does not typically change across projects, teams must be able to adapt to unique environments and conditions, as well as regional OSHA requirements. For example, while our “lock out and tag out system” is consistent across our projects, we finetune the process based on each location. Project elements can also influence factors like PPE, tooling and equipment, and ongoing maintenance, which in turn inform the training program.
For each project, EVLO prepares an emergency response plan that outlines high-level information and granular details on:
- Site layout
- Project partners and onsite personnel
- Location of and key contacts at the nearest fire department
- Precise location of battery safety shut-off switches and the proper sequence for shut-off
Once our gameplan is solidified, we provide hard-bound copies for quick reference and tour the site with local fire officials, ensuring everyone is fully informed and ready to take prompt action in the event of an emergency. We also recommend that our customers conduct regular inspections and maintenance of all systems to provide additional peace of mind.
Taking Training to the Next Level
As a subsidiary of Hydro-Québec, North America’s largest renewable energy producer, EVLO has unmatched insight and knowledge on safety. What’s more, EVLO’s world-class solutions are backed by decades of research and development.
However, we understand that project partners and key stakeholders might not be as well-versed in BESS safety – that’s why EVLO prioritizes comprehensive training and education for all involved.
EVLO’s training courses are led by a veteran team of industry experts. We ensure that all customer, internal, and external stakeholders are not only educated on our products but also informed on protocols tailored to their specific geographies and edge-case scenarios. In addition to general emergency measures, such as an evacuation plan in the event of an extreme weather event, each project includes a risk analysis that informs customized safety recommendations and procedures for a given site.
As global climates change, BESS function and safety in extreme temperatures is an increasingly critical consideration. EVLO’s batteries are rated to operate at temperatures from -40°C to 55°C, ensuring we can deliver the performance and reliability our customers demand in a wide range of environmental conditions.
We also have the real-world experience to back up these claims. From operation in remote sites like our Parent project to deployment in blizzards and sub-freezing temperatures, EVLO’s work in extreme climates gives us the confidence and expertise to implement and train workers on external safety contingencies that may arise from harsh weather or environmental conditions.
“My first unit deployment [with EVLO] was in Quaqtaq, one of Quebec’s northernmost inhabited villages. This deployment marked the first energy storage system of its kind, specifically designed to adapt to extreme cold temperatures down to -40° Celsius (-40° Fahrenheit).
Delivering reliable energy storage in such harsh conditions was a remarkable experience, helping the community transition to renewable energy and reduce dependency on fossil fuels.”
—Guillaume Labarthe, EVLO Principal Electrical Engineer
Innovation in Testing as the Industry Evolves
EVLO is advancing training beyond the classroom with its world-renowned 25 kV test line facility, where EVLO’s BESS are tested under real-world conditions to identify and develop protocols for unforeseen hazards, ensuring peak safety, reliability, and performance during deployment.
Moreover, we are currently using our test line to innovate and develop new training and safety best practices for the industry at large. Certifications and testing processes will continue to evolve as the technology matures, and we must ensure that safety protocols keep pace with these developments.
“In the next few years, [the industry is] going to have to elevate [its] game for health and safety to make sure everyone is at the same level. Training is going to be critical for long-term operation. This means, among other things, that workers can’t just do basic training; they must shadow experts to gain vital hands-on safety experience.”
—Cedric Fortin, EVLO Head of Product/Service Interaction
A Pathway to Progress Through Safety
At EVLO, we believe that a strong foundation in worker safety not only streamlines and improves efficiency, but ensures a sustainable, safe future for all.
Amid the industry’s rapid growth and innovation, we must strive to overachieve in safety and hold ourselves to higher standards. EVLO’s safety ethos is to remain flexible enough to adapt to unique project and environmental conditions while remaining rigid enough to ensure a consistently high standard of safety across all projects.
That’s the EVLO difference.