Blog
Ensuring Fire Safety in BESS
May 9, 2023
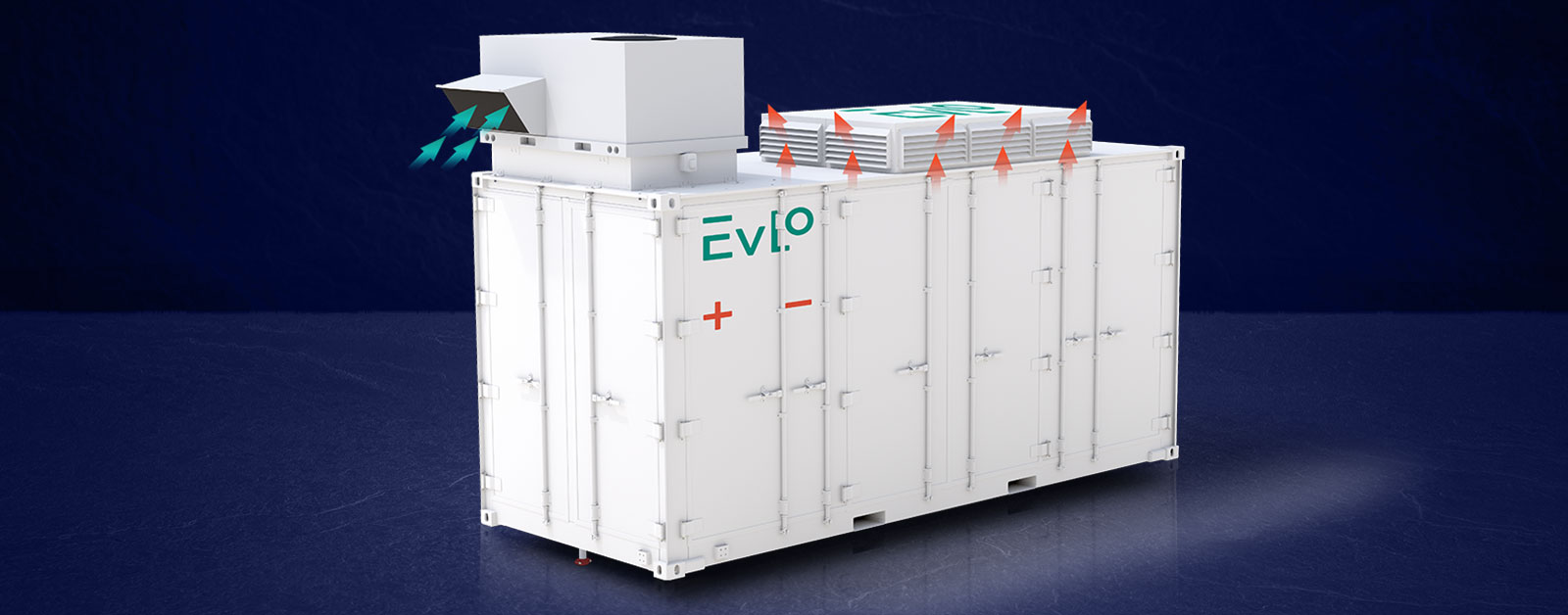
Leading-edge fire protection solutions at all levels
Evolving EVLO security technologies
As renewable energy sources like wind and solar continue to grow, utility-scale energy storage systems are essential to ensure that homes, communities, and businesses can rely on a dependable supply of clean electricity. Lithium batteries’ high energy density and long lifecycle make them a common choice for utilities to back up these renewable resources.
However, while we consider our lithium iron phosphate (LFP) battery chemistry to be safer than others, no battery is perfect and thermal runaway can, in rare cases, result in fires or explosions. This makes safety precautions paramount when designing battery energy storage systems (BESS). Certification bodies such as UL and NFPA are also raising battery safety standards for the benefit of the industry.
As a subsidiary of Hydro-Quebec, EVLO’s engineers are keenly aware of utilities’ needs regarding safety in BESS. We’ve developed a unique system of technical safety features at every level of our battery system: module, rack, and enclosure. From fire detection to thermal runaway prevention, our safety mechanisms both limit the risk of thermal runaway and, in case of an event, ensure that thermal propagation will be kept to a minimum and the event remains self-contained.
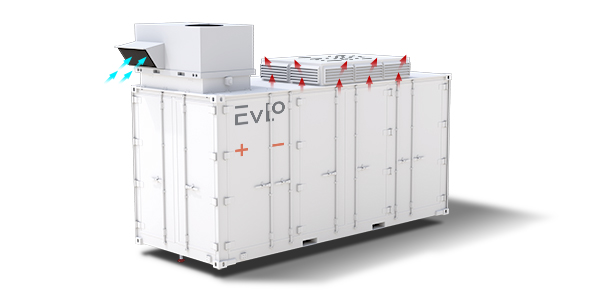
Utility-Grade Safety, by Utility Professionals
Working in collaboration with numerous globally respected and independent safety firms, we also conduct comprehensive and thorough analyses to provide further validation and confidence in our quest to build the safest BESS.
Fire Mitigation Measures at Each Level
Each tray contains up to six modules. At the module level, thermal barriers are installed between cells to slow down and prevent propagation to neighboring cells.
The tray level includes two forms of fire protection: double thermal barriers between each tray, and the arrangement of the trays themselves. The design creates an air gap between each tray. In case of thermal runaway, this gap functions as a chimney by providing a path for gas release that avoids contact with nearby trays, therefore limiting temperature increase on neighboring modules.
At the enclosure level, there are hundreds of sensors as well as proprietary-designed venting panels. Once these sensors detect excess heat, smoke, or hydrogen, they trigger the active mitigation plan: the HVAC goes into Economizer Mode and forces fresh air in from outside the enclosure. Simultaneously, the venting panels open to release hot gas from the enclosure.
This system works even during power outages, since the venting panels include a failsafe mechanism. In this condition, natural convection alone is enough the meet the performance requirements of NFPA 69.
Why We Chose a Layered Approach to Fire Safety

Deflagration panels are sheets of metal that open and release pressure in case of an explosion. This method requires that the container’s design withstand the initial pressure buildup, which ultimately tears the deflagration panel apart and releases the pressure. The process still allows an explosion, which doesn’t allow for individual unit testing (because the process would destroy that unit). The resulting destruction makes it impossible to ensure that this method will work as intended for each unit.
These drawbacks led us to base our fire mitigation approach on NFPA 69, which makes use of sensors, can be tested on a unit-by-unit basis, and is designed to prevent explosions. Our approach also goes beyond NFPA 69’s requirements because we add passive fire mitigation elements on top of our active strategies. Namely, the failsafe venting panels open by themselves to release pressure even during a power outage. We call this approach NFPA 69++.
Our fire mitigation designs also offer flexibility depending on users’ different preferences and requirements. For example, some may need extra sensors, while others may want a different type of detection sensors depending on their climate or requirements. Our engineers can adapt these to meet the most stringent safety standards.
The Most Thorough BESS Fire Prevention Testing Possible
The UL 9540A test procedure is a set of tests for each succeeding level: cell, module, unit, and system. Currently, the minimum level lithium-ion batteries must pass is the unit level, so many lithium batteries are only tested up to that level. However, this level does not provide a full engineering validation because it doesn’t test all the safety features that must be implemented to meet the requirements of NFPA 855 68 and 69 sections.
Testing only up to the unit level also doesn’t reflect all aspects of the real-life conditions within a BESS enclosure. A BESS’s Fire Safety System depends on relationships between the cell, the module, the unit, the enclosure , detection hardware, mitigation hardware, and software. That’s why we have developed our own Engineering Validation Plan consisting of a large scale fire test on a fully functional enclosure following UL 9540A system-level guidelines.This test validates the performance as well as active, passive and gas ignition modes.
So for us, UL 9540A testing is just one part of the complete Engineering Validation Plan that we provide for our products. Testing the entire system in real-life conditions ensures that our fire mitigation measures will perform reliably on our customer’s sites under any circumstances.
Keeping Firefighters Safe with Distant Fire Resolution
In most cases, our mitigation strategies end thermal runaway by evacuating gasses via the opened vent ing panels. The fire resolves itself without any need for extinguishing agents such as water, and operators can then replace the module and fuse to regain a functional system.
With this solution, firefighters aren’t usually needed onsite as the fire is fully contained.
However, to provide maximum flexibility in safety measures, we also offer an optional dry pipe system inside the container. These pipes allow firefighters to connect to the Fire Department Connection (FDC) located away from the enclosure. Once the water’s connected, it spreads sufficiently throughout the enclosure without flooding it. This limits the temperature rise and prevents the fire from spreading to nearby enclosures. If customers desire additional measures, the dry pipe option provides an extra layer of safety by enabling first responders to deal with out-of-control fires while keeping a safe distance and maintaining personnel safety.
BESS Systems That Put Safety First
From product design through testing and performance, we’ve worked to make EVLO’s BESS solutions the safest possible. Designed by engineers with extensive experience in utility environment and module design, they incorporate tailored fire mitigation measures from the module through the enclosure level. In addition to active mitigation measures that surpass NFPA 69 requirements, we’ve included passive measures that work even during loss of auxiliary power. Extensive field testing, including full engineering validation, helps ensure that EVLO’s BESS solutions offer an unparalleled level of safety and reliability for our customers.
À propos de l'auteur
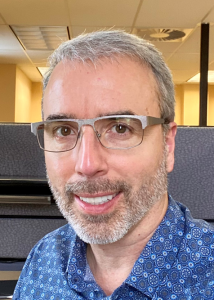
Eric Latulipe
Ingénieur mécanique
Eric Latulipe a joint EVLO en 2020 en tant qu’ingénieur mécanicien. À ce titre, il joue également le rôle d’expert en présentant les derniers produits EVLO. Auparavant, Eric a travaillé pour Pratt & Whitney et Dana TM4, où il a acquis une expérience précieuse dans le domaine des technologies électriques et hybrides. Au cours de sa carrière, il a collaboré à plusieurs projets internationaux. Animé d’un vif intérêt pour l’innovation, en particulier pour les caractéristiques de sécurité du stockage de l’énergie, il est un gestionnaire de projet, un négociateur et un chef d’équipe accompli. L’expertise, la créativité et les capacités de résolution de problèmes d’Eric sont les fondements de son travail. La liste de ses réalisations est longue, et il est notamment titulaire de 15 brevets.